The thermal management of electric motors is an essential element in competitive low-carbon mobility, since more efficient cooling not only increases motor performance density (power or torque by mass), but also improves operational reliability by preventing deterioration phenomena (such as demagnetization). Also, oil injection on the most thermally stressed parts (e.g. stator coil heads) appears to be a promising solution for improving the cooling performance.
The development of such systems must be based on optimum design and sizing, which requires detailed knowledge of heat exchange and convection coefficients between the liquid and the components to be cooled. Moreover, the oils used for cooling electrical machines have special properties (high Prandtl number1) which lead to large differences between the characteristic scales of flow (> 1/10 mm) and heat (< 1/10 mm), making it difficult to understand the phenomena and predict them using numerical simulations. In addition, the data currently available comes from tests with water-impact jets, and is therefore not representative of the situation currently under consideration.
To overcome this lack of data, a basic experiment with a simplified configuration, in which the oil is sprayed onto a heated flat plate (figure 1a), was developed and carried out to precisely characterize convective heat transfer in this configuration [1]. Surface temperature was recorded using high-precision thermocouples, and advanced optical fluorescence techniques were deployed so as to simultaneously obtain local temperature and oil film thickness. Combining the experimental data obtained with numerical simulation results of heat conduction in the plate made it possible to characterize the overall thermal behaviour, and in particular the local heat flux extracted from the plate (Figure 1b).
This methodology was developed and used in a thesis2 with the aim of characterizing heat dissipation during the interaction of a liquid jet with a hot plate, as a function of operating conditions (injection rate, oil temperature, etc.). The tests completed in this manner led to the development of empirical correlations between these parameters, which are extremely useful for the design of new electrical machines.
The same methodology will now be applied to cases closer to the application under consideration, such as complex geometries like windings, in order to generate new empirical correlations. These will be essential to the development of reliable and representative models to describe fluid flow and heat exchange in electric motors, while limiting calculation times for design offices.
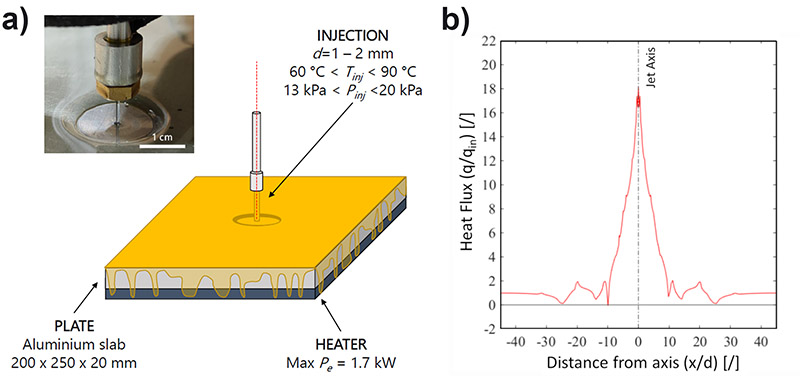
1.a Experimental configuration of a liquid jet impacting a hot plate.
1.b Result of the developed methodology, characterization of the heat flux extracted by the impact of the jet on the plate.
1- Dimensionless number, defined as the ratio between kinematic viscosity (related to movement quality) and thermal diffusivity (related to quantity of heat).
2- Entitled “Développement d'une méthodologie expérimentale pour caractériser les systèmes de refroidissement par liquide des moteurs électriques”.
Bibliographic reference
-
Cornacchia, I., Pilla, G., Chareyron, B., Bruneaux, G., Kaiser, S., Poubeau, A. (2021, May). Development of an Experimental Methodology to Characterize Liquid Cooling Systems for Electric Motors. In 2021 IEEE International Electric Machines & Drives Conference (IEMDC) (pp. 1-7). IEEE.
>> https://doi.org/10.1109/IEMDC47953.2021.9449572
Scientific contact: michele.bardi@ifpen.fr