As part of the 2021-2027 State-Region Plan Contract, the PROPRE1 project aims to create a favorable ecosystem to intensify innovation in the field of chemical recycling of plastics2. Led by IFPEN and UCBL3, the objective of the project is to design and make available a set of differentiating tools for work ranging from fundamental research (TRL 1 to 3) to industrial development (TRL 4 to 7). This continuum of tools will make it possible to concretize laboratory concepts on a pilot scale and to produce representative loads to convince industrialists to move towards development. This article concerns pilot-scale tools (TRL 4 to 7) carried and located on the IFPEN-Lyon site and whose access to the ecosystem will be ensured by the Axel’One collaborative platform.

The design of pilot-scale tools (TRL 4 to 7) for this project represents a major engineering challenge for which IFPEN's scientific and technical expertise in the field of processes was essential. In addition, this project required precise anticipation of the needs of future user projects and the harmonious integration of the various technologies selected.
The PROPRE pilot-scale platform has been designed to be both modular and scalable, with semi-industrial-sized equipment, adapted to the advanced recycling of plastics.
1 Financed by the French State, the Auvergne-Rhône Alpes region, Lyon Metropolis, IFPEN, CNRS and UCBL (total budget of €9.5 million), supported by the competitiveness clusters Axelera, Polymeris, Techtera, the eco-organization CITEO and the Lyon Polymers Science and Engineering (LPSE) consortium)
2 Recycling involves physicochemical steps that complement mechanical recycling by transforming plastic waste into secondary raw materials. These are then reintroduced at different stages of the plastic production process through more or less short loops.
3 Claude Bernard Lyon University
Cutting-edge infrastructure
The PROPRE project has evolved through several key steps since its launch. In 2024, a co- and counter-rotating twin-screw extruder for melting and injecting plastic feeds was installed in a dedicated ATEX4 space, specially built to accommodate large-scale projects with potentially substantial quantities of solvents.
In early 2025, three stirred reactors with different volumes (1, 7 and 50 liters) were received, enabling batch or continuous production, as required, of between 100 kg and 1 metric ton of recycled plastic. These reactors are designed to operate at high temperatures and pressures, which are the operating conditions required for most of the projects concerned.
4 Meeting the regulations governing potentially explosive atmospheres
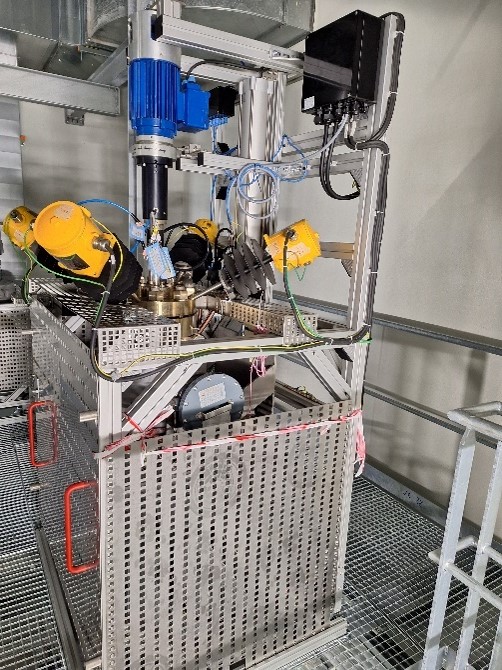
At the same time, three decanters of 7, 16 and 36 liters were received and installed. They play a crucial role in separating insolubles (pigments, polymers, fibers, etc.) and purifying impurities.
The 36-liter decanter is designed to operate either horizontally or vertically, to enable the separation of low- and high-density molecules respectively.
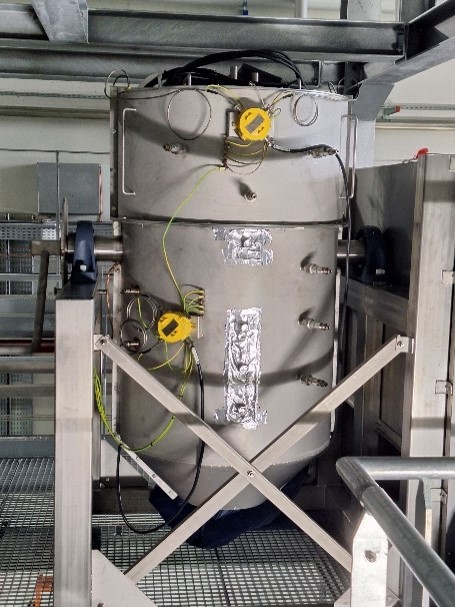
Additional equipment coming soon
To further strengthen the platform's capabilities, other tools are currently being procured:
- an SMB5 for highly optimized adsorption purification
- specific distillation for polymer and solvent separation;
- a centrifugal decanter that extracts fine particles to a high level of purity and reduces separation time;
- liquid/liquid extraction for advanced purification of elements in the liquid phase;
- and filters based on various technologies, designed to separate impurities and insolubles, or to separate polymers from waste solvents.
Once operational, this equipment will optimize recycling processes to improve the quality of the resulting products. Compatibility between the various pieces of equipment has been taken into account (flows, temperature, automation language) to ensure a smooth, efficient sequence of individual steps.
5 Simulated moving bed: used to achieve high purity, high efficiency and quasi-continuous operation thanks to cyclic valve switching and an operating range restricted to maximum adsorbent performance
A modular platform
The tools making up the PROPRE platform of IFPEN’s site have been designed to meet the needs of the different operations involved in plastics recycling and can be adapted to various types of plastics and processes. Modularity enables users to configure the equipment as a function of their specific needs.
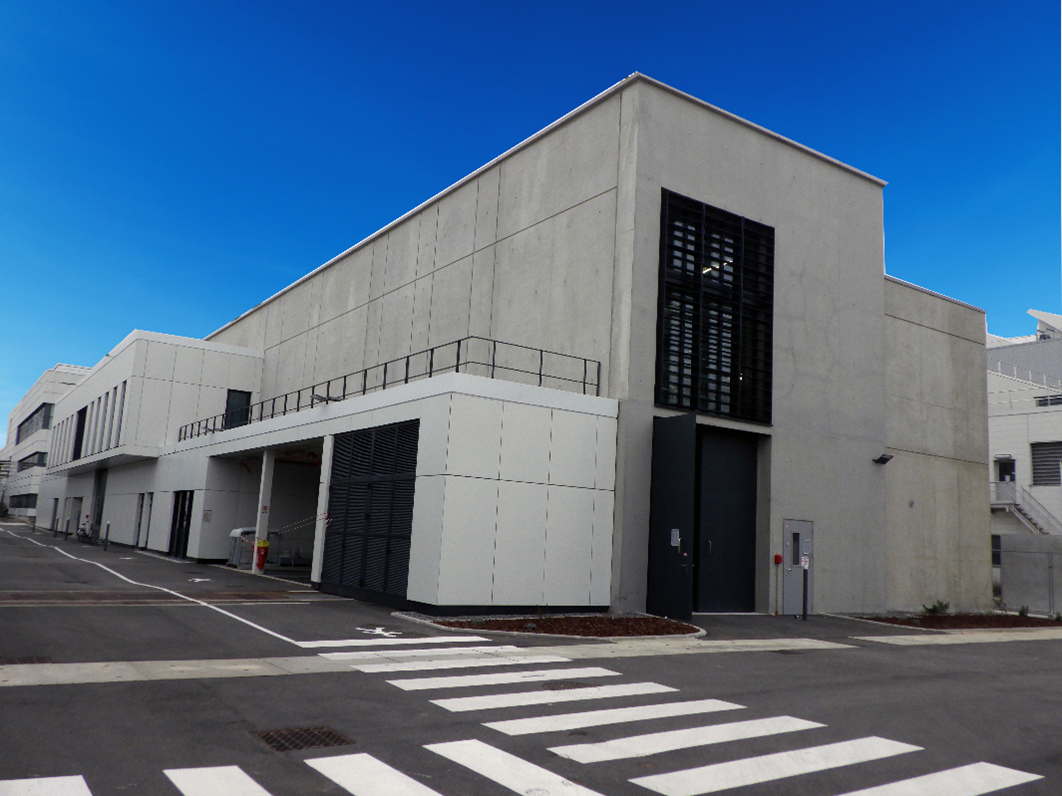
The platform is modular to support projects as they scale up, allowing sufficient sampling (around 1 metric ton) for industrial-scale shaping or re-polymerization trials. Equipment will be regularly upgraded or can be easily replaced to keep pace with technological advances.
The PROPRE project is already attracting a great deal of interest from numerous players in the sector. Several projects are in the pipeline, testifying to the relevance and importance of this initiative. The platform promises to become a genuine catalyst for innovation in the chemical recycling of plastics.
Scientific contacts for the pilot-scale tools: Aline GREZAUD et Denis GUILLAUME (IFPEN)
Scientific contact for the discovery-scale tools: Vincent MONTEIL (UCBL)