25.03.2019
5 minutes of reading
According to the IPCC (Intergovernmental Panel on Climate Change), restricting global warming to 2°C requires a reduction in greenhouse gas emissions of between 40 and 70% over the period from 2010 to 2050.
In a context of increasing energy demand, CCS (CO2 capture and storage) is a technique that has to be implemented to minimize the emission of CO2 generated by fuel burning. The last few years have also seen the emergence of technologies such as CCU (CO2 capture and utilization), giving the operation an added economic value.
One of the technologies under consideration for the capture aspect is Chemical Looping Combustion (CLC), a new promising process making it possible to burn fossil fuels while capturing the CO2 emitted, with a relatively low energy penalty.
The process is hinged around the circulation of oxygen-carrying materials between two reactors (figure 1). The oxygen required for fuel oxidation is provided by the oxygen carrier in the fuel reactor, and then the reduced oxygen carrier is re-oxidized by air in the air reactor. A flow of CO2 and steam (that can be easily separated) is thus obtained at the fuel reactor outlet.
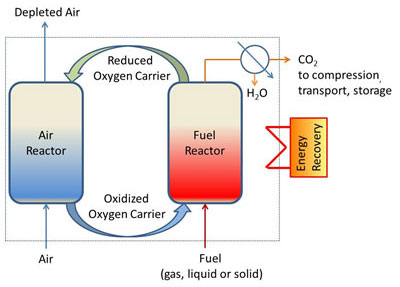
The most widely researched version of this combustion process is that of the circulating fluidized bed. Several pilot units, of various sizes and designs, are currently operational around the world, requiring the use of a material that closely meets the needs of the CLC process in terms of particle size (100-300 µm), oxygen transfer capacity, reactivity and physical-chemical stability in operating conditions.
Numerous synthetic materials, various natural ores and even some forms of industrial waste have been used in the past as oxygen carriers with a degree of success, both in terms of their oxygen transfer capacity and their reactivity. However, in the majority of cases, they have been studied using a number of redox cycles that is not sufficient to produce and characterize any degradation.
It has been demonstrated[1] that the use of cheap natural ores, such as ilmenite, for the combustion of coal-type solid feeds is feasible. However, the low oxygen transfer capacity and reaction kinetics demand sizable facilities, and the risks related to agglomeration or attrition are high. It is therefore important to also have access to synthetic oxygen-carrying materials likely, despite being more expensive, to minimize the cost price in terms of both CAPEX and OPEX.
Synthetic materials are generally made up of an active phase (a metal oxide that reacts with the fuel, chosen from Mn, Fe, Co, Ni or Cu oxides), and a binding phase (oxide that is stable in the conditions of the process, for example Al2O3 or SiO2) making it possible to increase the mechanical resistance of the particles.
Within the framework of the European SUCCESS project, a promising copper oxide-based oxygen carrier supported on alumina was tested at IFPEN on a 10kWth CLC pilot unit, with a view to studying its ageing(1). Tests using methane (CH4) as a fuel led to the observations in figure 2.
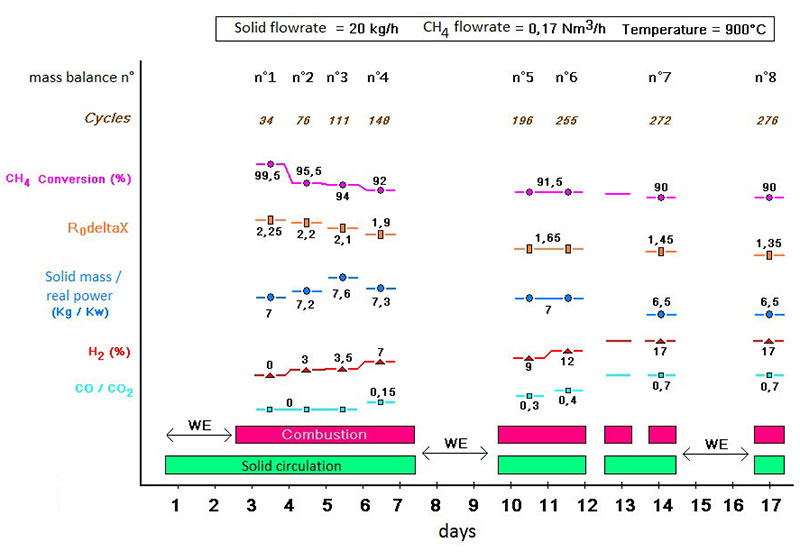
(R0DeltaX quantity of oxygen released by the material)
Initially, all of the injected methane is converted into CO2 and water by the copper oxide supported on alumina. A rapid deactivation of the latter is nevertheless observed, resulting in a reduction in methane conversion and the appearance of CO and H2 in the outlet gas.
X-ray diffraction analysis of samples of the oxygen-carrying particles taken during the test (in oxidized form) shows a gradual but significant evolution of the crystallographic phases forming these particles, changing from a mixture of tenorite (CuO) dispersed in a γ-alumina matrix to a mixture of tenorite, copper aluminate CuAl2O4 and α-alumina (figure 3).
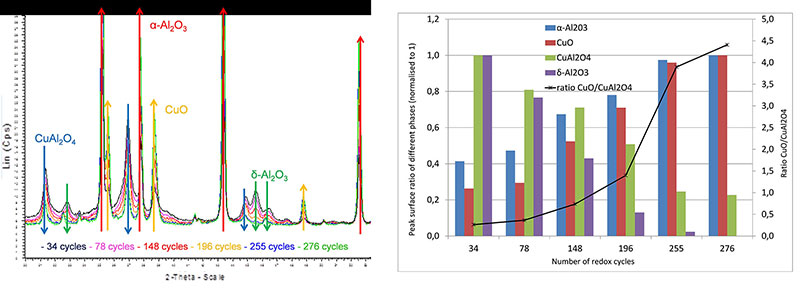
Moreover, SEM observation of the same particles (figure 4) shows that the accumulation of redox cycles leads to significant copper mobility, as well as the appearance of fractures within the alumina matrix. As well as a compromised life span due to fracturing, the sintering of the copper is likely to be the source of the observed deactivation.
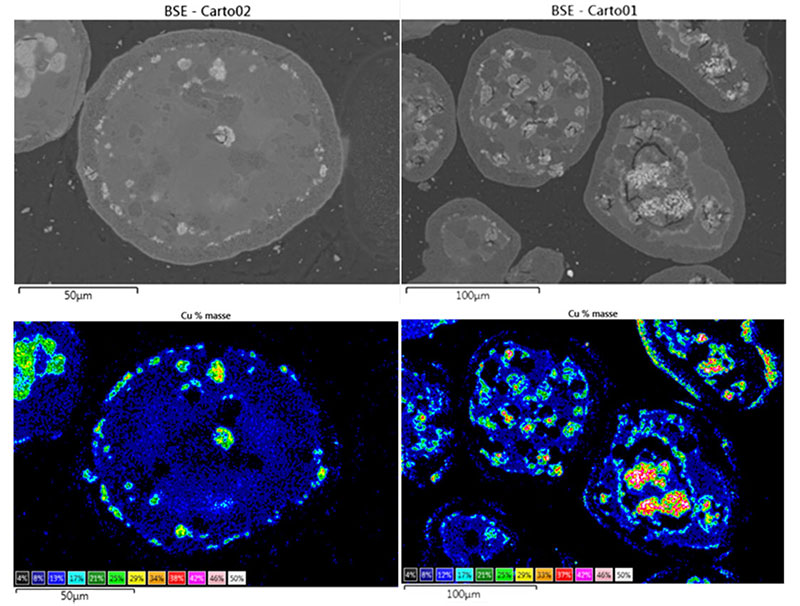
The collaborative research conducted by IFPEN has led to progress in our understanding of the degradation mechanisms of these materials, as well as in methods for their characterization (figure 5), invaluable elements in the quest for solutions adapted to this promising technology in terms of tackling climate change.
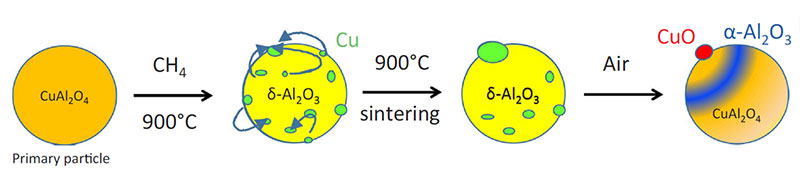
Scientific contacts: arnold.lambert@ifpen.fr - stephane.bertholin@ifpen.fr
(1) For example within the framework of the European ENCAP project, involving IFPEN
Publication
[1] A. Lambert, A. Tilland, W. Pelletant, S. Bertholin, F. Moreau, I. Clemençon, M. Yazdanpanah, Performance and degradation mechanisms of CLC particles produced by industrial methods, Fuel 216 (2018) 71
>> https://www.deepdyve.com/lp/elsevier