06.07.2021
5 minutes of reading
Li-ion batteries are omnipresent in our day-to-day lives, from mobile applications to connected tools via micro-mobility systems (e-scooters, e-bikes, etc.). The widespread roll-out of electric vehicles is encouraging this trend and accentuating safety challenges related to the use of such systems. Predicting the initiation and propagation of thermal runaway, the most feared phenomenon for this type of battery, is thus of considerable interest to battery pack manufacturers, integrators and users. After eight years of development research, IFPEN offers solutions based on modeling and simulation.
Thermal runaway: origin and mechanisms at work
In terms of safety, lithium-ion batteries carry much greater risks than traditional aqueous electrolyte batteries, such as lead-acid batteries. Firstly, their electrolyte is made up of a fluoride salt dissolved in a volatile and inflammable organic solvent. Secondly, the active materials present in their electrodes are highly reactive at high temperatures [1].
An increase in temperature (figure 1) may have several causes: incident on a battery cell (crushing or perforation leading to an internal short-circuit, contact with a flame or excessive heat), incorrect use (overcharge, over-discharge, external short-circuit, etc.), or internal manufacturing defect (perforated separator).
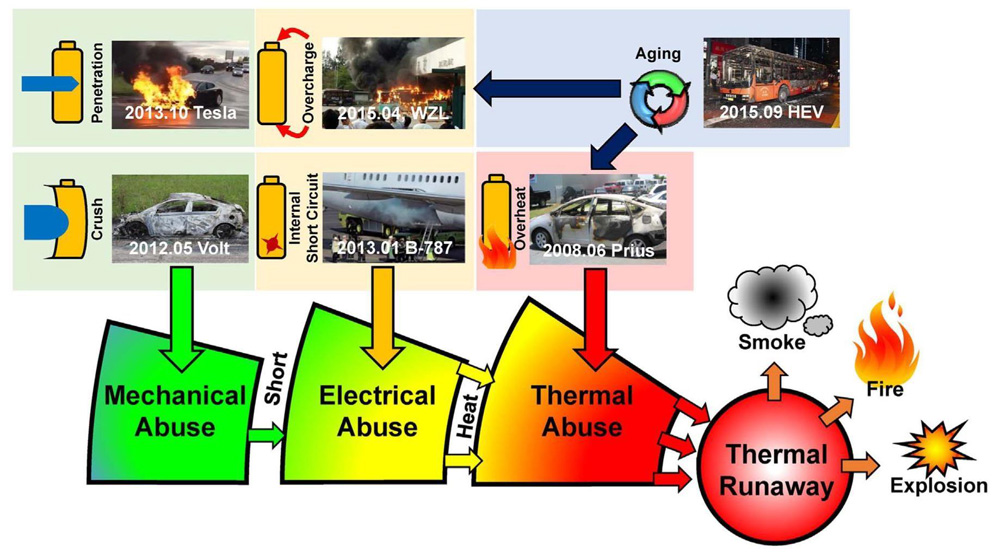
In turn, this heating triggers chemical decomposition exothermic reactions that occur at the various internal components: SEI (Solid Electrolyte Interphase), electrolyte, negative and positive electrodes, etc. If the heat produced is in excess to the heat dissipated, these exothermic reactions continue, causing a cascading process, and the system become self-heating, leading to an uncontrollable rise in temperature (figure 2). Due to the fact that it is sealed, the pressure in the cell rises until venting, the cell opens to release the electrolyte in the form of inflammable gases, generally leading to fire and toxic fumes as a result of the presence of fluoride compounds.
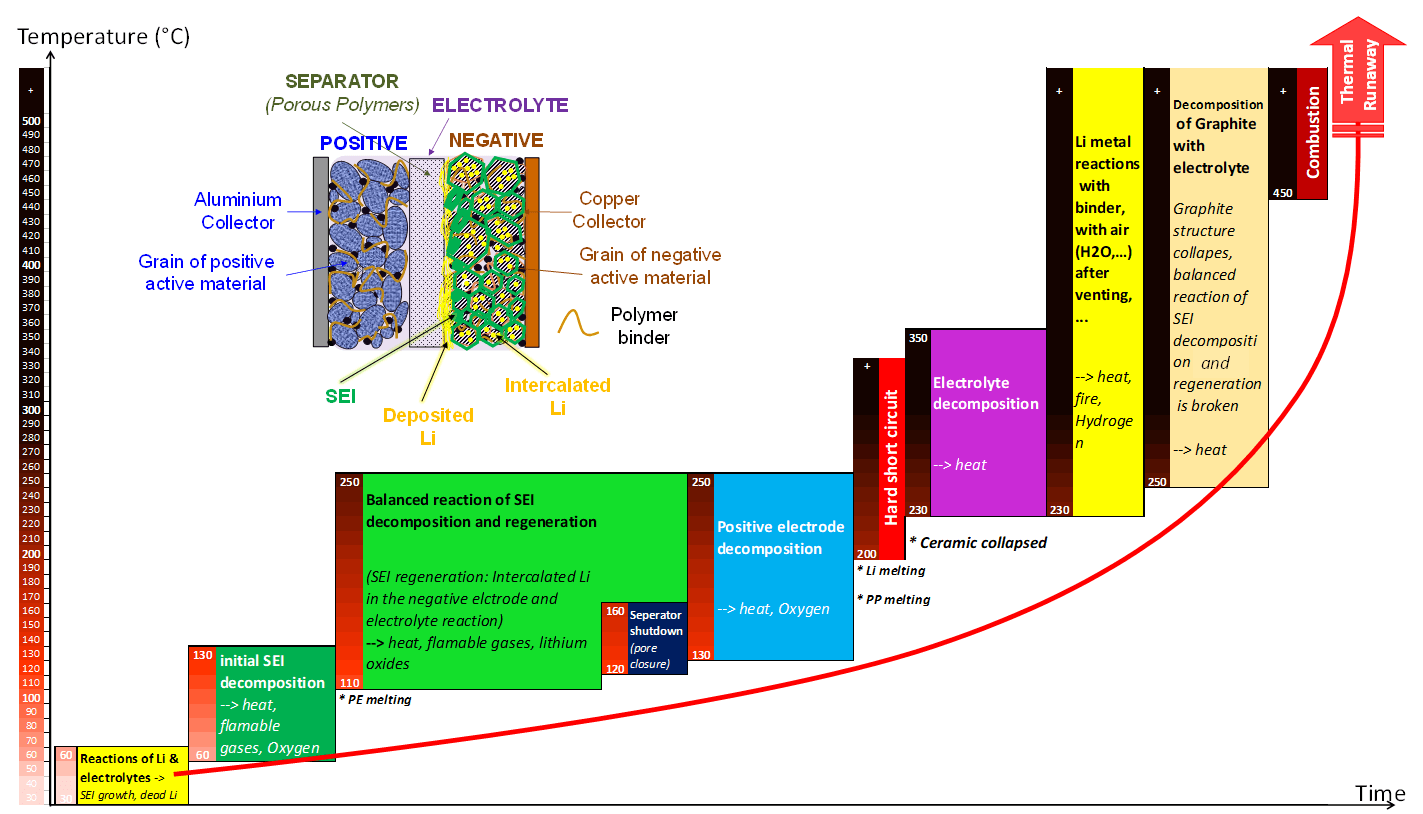
Battery packs are made up of an assembly of dozens of cells positioned next to each other, in such a way that thermal runaway initiated in one cell gradually spreads to neighboring cells. This cascading propagation which is difficult to control once triggered, is much feared and manufacturers therefore take every possible precaution to prevent it, starting at the design stage.
Modeling to describe the thermal runaway phenomenon
To study this phenomenon and evaluate the safety of a lithium-ion battery, industrial players conduct a series of “abuse” tests on dedicated platforms1 . However, these are complex, time-consuming and expensive, especially since they irremediably lead to the destruction of the samples studied.
Over the last fifteen years or so, IFPEN’s Electrochemicals and Materials Department has been developing numerical models and simulation tools aimed at predicting and describing the nominal operation (electrical and thermal behavior) and behavior during ageing (evolution of performance-related parameters) of batteries2. They are widely used by the sector’s industrial players as a “battery pack” system design and study tool, particularly for electric vehicles. It was thus a logical step for IFPEN to develop research concerning thermal runaway simulation, adding the safety aspect to existing tools.
Launched with INERIS in 2013 via a first PhD project [4, 5] and continued via a second one [6], this research was also conducted within the framework of the European DEMOBASE project coordinated by SAFT (2017-20) [7] , leading in 2018 to the first commercial version of a “thermal runaway model”. This model is able to simulate the evolution of the heat released by the cell, the evolution of the cell’s internal pressure and the evolution of the cell’s voltage when operating under abuse conditions (figure 3).

It takes into account the principal successive phenomena occurring within a lithium-ion battery cell during thermal runaway (see figure 2) : the cascade of thermochemical decomposition reactions affecting the various components, as well as internal physical damage, such as the separator melting (leading to an internal short circuit that releases additional energy) and rupture of the vent or packaging leading to the release of pressurized gases [8].
The events considered in the model as being able to initiate the thermal runaway process are an overheat, an external short circuit or battery overcharge. A new PhD project (2021-24) in partnership with the LRCS (Solid Reactivity and Chemistry Laboratory) will be aimed at completing this events list, the objective is to understand and model the internal short-circuit initiation event, frequent in the event of a manufacturing defect.
Finally, since the model is integrated into the global simulation of battery operation (nominal and ageing behavior), it now makes it possible to predict the initiation and severity of thermal runaway as a function of the chemical nature of the components of the lithium-ion battery, its use conditions and degree of aging.
Simulation as a design tool for safe battery packs
The simulation tools developed by IFPEN integrate a physical model of the different phenomena taking place in the cell and contribute to improved battery pack safety by enabling manufacturers to more easily study a broad range of solutions during the pre-design stages. For a given pack, it is easy to develop a simulator from a cells model integrating their thermal runaway submodel.
Choices in terms of design (spacing and positioning of cells, materials used, presence of a safety device such as a firewall, etc.) or management (thermal, electrical, etc.) can then be explored in parametric studies based on numerical simulation, which are very quick due to the simplicity of the underlying models. If necessary, there then follows an in-depth look at the best solutions based on prototyping or 3D simulation approaches, resulting in savings in terms of time and the number of tests required.
This global approach was implemented and validated within the framework of the European DEMOBASE project (figure 4) and continues to attract interest from industrial players for developments.
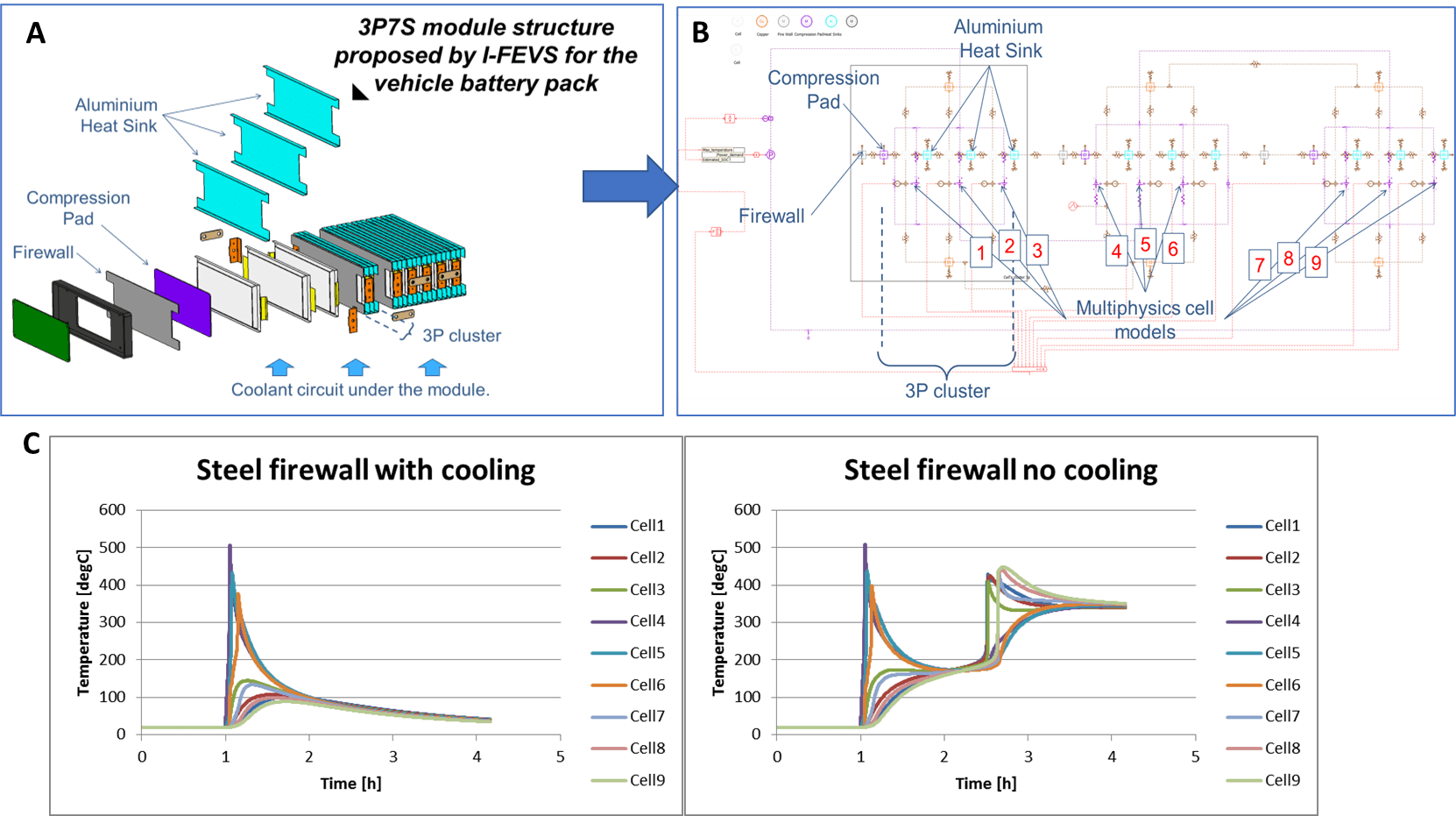
1. Such as that of the INERIS (French National Institute for Industrial Environment and Risks) https://prestations.ineris.fr/fr/solutions-thematiques/moyens-essais-remarquables/plateformes-essais/plateforme-moyens-essais-dedies
2. Today, these tools are marketed in the Electrical Storage library of the Simcenter Amesim system simulation software developed by SISW (Siemens Industry Software).
https://www.plm.automation.siemens.com/global/fr/products/simcenter/simcenter-amesim.html
3. https://www.demobase-project.eu/
4. HWS (Heat Wait and Search) test using ARC (Accelerating Rate Calorimeter)
Scientific contact: Julien Bernard
Références
[1] Abada S., Marlair G., Lecocq A., Petit M., Sauvant-Moynot V., Huet F. (2016) Safety focused modeling of lithium-ion batteries: A review, Journal of Power Sources 306, 178–192. DOI: 10.1016/j.jpowsour.2015.11.100.
[2] Feng X., Ouyang M., Liu X., Lu L., Xia Y., He X. (2018) Thermal runaway mechanism of lithium ion battery for electric vehicles: A review, Energy Storage Materials 10, 246–267. DOI: 10.1016/j.ensm.2017.05.013.
[3] Nguyen T.T.D., Abada S., Lecocq A., Bernard J., Petit M., Marlair G., Grugeon S., Laruelle S. (2019) Understanding the Thermal Runaway of Ni-Rich Lithium-Ion Batteries, WEVJ 10, 4, 79. DOI: 10.3390/wevj10040079.
[4] Abada S., Compréhension et modélisation de l'emballement thermique de batteries Li-ion neuves et vieillies (Understanding and modeling thermal runaway of new and aged Li-ion batteries), PhD thesis defended on 14/12/2016 within the École doctorale Chimie physique et chimie analytique de Paris Centre (Paris Centre Doctoral School for Physical and Analytical Chemistry), in partnership with IFPEN, INERIS and LISE (Laboratoire Interfaces et Systèmes Electrochimiques, the Interface and Electrochemical System Laboratory).
[5] Abada S., Petit M., Lecocq A., Marlair G., Sauvant-Moynot V., Huet F. (2018) Combined experimental and modeling approaches of the thermal runaway of fresh and aged lithium-ion batteries, Journal of Power Sources 399, 264–273. DOI: 10.1016/j.jpowsour.2018.07.094.
[6] Nguyen Thi Thu Dieu, Understanding and modelling the Thermal runaway of Li-ion batteries, thèse de doctorat soutenue le 04/02/2021 dans le cadre de l’école doctorale en Sciences Technologie et Santé de l’Université de Picardie Jules Verne, en partenariat avec IFPEN, l’ INERIS et le LRCS (Laboratoire de Réactivité et Chimie des Solides).
[7] Petit M., Abada S., Mingant R., Bernard J., Desprez P., Perlo P., Marlair G. (2019). Demobase project: Numerical simulation for seamless integration of battery pack in light electric vehicle, 32nd EVS32, Lyon, France, May 19-22,2019. https://zenodo.org/record/3368893
[8] Petit M, Marlair G, Abada S, Wang C-Y (2019) Safety tests for Li-secondary batteries-Modeling of safety tests and events: Chapter 10B in Electrochemical Power Sources: Fundamentals, Systems and Applications - Li-Battery safety (Eds.: J. Garche & K Brandt), Elsevier.