CO2 capture, use and storage (CCUS) technology consists in capturing CO2 from its source of production, using it and storing it in an underground facility. It is of interest to industrial players since it would enable them to significantly reduce their CO2 emissions. But this promising solution still has to demonstrate that its implementation on an industrial scale is feasible at a reasonable cost.
- CCUS: an action lever for the climate
- What sources of CO2 emissions can be captured, used and stored?
- The challenges of CCUS
- CO2 capture from industrial sources
- CO2 capture in the atmosphere
- Transporting CO2
- CO2 storage
- CO2 conversion, a better solution than capture?
CCUS: AN ACTION LEVER for the climate
Global greenhouse gas reduction scenarios highlight the role of CCUS in the energy mix.
In the Net Zero Emission by 2050 (NZE) scenario, published in 2021, the International Energy Agency estimates that in order to achieve carbon neutrality by 2050, 7.6 Gt of CO2 will have to be captured annually from 2050, i.e., 20% of current emissions. An intermediate objective fixes the quantity of carbon dioxide that will have to be captured at 1.6 Gt from 2030. This quantity increases to 4 Gt of CO2 in 2035, i.e., a factor of 100 to be achieved in less than 15 years.
To achieve the 2°C objective, according to the IEA’s “sustainable development” scenario, more than 100 billion tonnes of CO2 would have to be stored and thousands of CCUS facilities rolled out by 2050. Today, about thirty large-scale facilities are operational worldwide, injecting some 40 million tonnes of CO2 per year.
Industrial players are taking an interest in the technology as the only solution likely to enable them to significantly reduce the carbon footprint of their activities. In 2016, 13 major oil companies created a one billion dollar fund, the Oil & Gas Climate Initiative, aimed at developing technologies to reduce CO2 emissions, including CCUS, which is considered to be indispensable. In addition, Equinor, Shell and TotalEnergies are contributing a combined investment of €640 million to the Northern Lights project aimed at storing 1.5 million tons of CO₂ per year beneath the North Sea bed, at a depth of 2,600 meters, by 2024. Liquefied CO₂ will be transported by pipeline and ship.
What sources of CO2 emissions can be captured, USED AND stored?
CCUS concerns industrial sources where emissions are geographically concentrated. The rapid development of renewable energies limits the scope of CCUS for electricity production, which has already embraced the decarbonization process, with the exception of countries like India and China where CO2 capture is essential in order to achieve carbon neutrality. However, many heavy industries (steel-making, cement plants, refining, chemicals and petrochemicals) do not have yet access to substitution technologies enabling them to reduce their CO2 emissions to any significant degree.
CCUS also has the capacity to capture CO2 directly in the atmosphere.
The challenges of CCUS
CCUS is not a new technology: CO2 capture and separation techniques have been applied in industry for decades, and CO2 injection has been used since the 1970s for enhanced oil recovery and CO2 is a raw material used in some industrial sectors. But greenhouse gas emission reduction objectives require the creation of a dedicated CCUS industry, which will mean very large-scale capture facilities, the mass development of transport networks, very extensive infrastructures for storage and a considerable industrial sector to convert CO2 into synthetic fuels and other high added-value products.
Numerous challenges will have to be overcome prior to deployment on such a scale, including:
- the reduction of the costs of capture, the most expensive step in the CCUS chain;
- the demonstration of large-scale CO2 storage capacities of CO2 in deep saline aquifers, and ensuring the confinement of CO2 and the safety of its storage over very long periods (several hundreds of years) in geological storage structures.
- the demonstration of high-capacity CO2 conversion processes at a reasonable cost.
CO2 capture FROM INDUSTRIAL SOURCES
This step can account for up to 70% of the process in terms of cost and represents a major technological and economic challenge. Three CO2 capture technologies in industry are under consideration:
• pre-combustion capture consists in decarbonizing the fuel before it is burnt, converting it into synthetic gas made up of hydrogen, water and carbon monoxide, and then adding steam to this synthetic gas. The resulting reaction causes the carbon monoxide to be converted into CO2, with the additional production of hydrogen. The CO2 and hydrogen are then separated using a solvent. The CO2 can thus be captured at this stage. Hydrogen, used alone, produces energy without CO2 emissions. This technology is currently considered to be too expensive.
- capture from "post-combustion" flue gases consists in recovering the CO2 by cleaning the flue gases emitted by combustion with a solvent. CO2 capture techniques exist that are well known and employed in the treatment of natural gas, whose CO2 concentrations are regulated. The facilities required for cleaning combustion flue gases are extremely expensive and consume considerable amounts of energy. Innovative options for capturing flue gas CO2 are being considered with a view to minimizing energy consumption and reducing the size of facilities and investments.
- oxycombustion capture consists in burning carbon-based fuels in the presence of pure oxygen instead of air, making it possible to obtain flue gases with a heavier CO2 concentration (around 90%). The latter is then easier to separate from the steam it is mixed with. The main problem relates to the cost of producing pure oxygen, which is generally obtained via cryogenic distillation of air. An alternative, cheaper method of producing oxygen is under consideration: "Chemical Looping Combustion" (CLC).
The "Chemical Looping Combustion" process
This process is based on the use of metal oxides for the purposes of combustion in the absence of nitrogen. When metal particles become oxidized, oxygen can be transferred to the combustion zone, thereby separating oxygen from nitrogen. This principle should make it possible to significantly reduce capture costs provided the associated technological challenges are overcome.
The technology is being developed by IFPEN in partnership with Total.
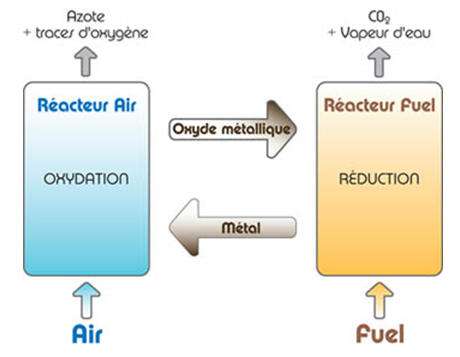
At present, existing facilities are only suitable for post-combustion flue gas capture. Chemical Looping requires design changes to facilities, representing a substantial financial investment but making it possible to obtain a very low energy penalty for CO2 capture.
CO2 capture and separation have been applied in industry for decades.
NEGATIVE CO2 EMISSIONS ?
Industrial processes exist that generate CO2 without recourse to fossil energies. One such example is ethanol production based on biomass fermentation. In this case, if the CO2 produced is captured and sent to a geological storage site, this CO2 derived from biomass will not return to the atmosphere: the CO2 emission is thus negative. Generally speaking, technologies making it possible to extract bioenergy from biomass while capturing and storing carbon, thereby removing it from the atmosphere, are referred to under the umbrella term BECCS (Bio-energy with carbon capture and storage). In 2022, at least five facilities around the world are using BECCS technologies and capturing around 1.5 million metric tons of CO2 per year.
CO2 capture IN THE ATMOSPHERE
Rather than capturing CO2 in flue gases where it is concentrated, it is also possible to capture it directly in the atmosphere where it is far more diluted, which means costs are much higher. Fifteen direct capture facilities are currently in operation around the world, capturing more than 9,000 tons of CO2 annually. There are two types of DAC (Direct Air Capture) technologies. In liquid DAC systems, the air is passed through a chemical solution, such as a hydroxide solution, which eliminates the CO2 while releasing the residual air into the atmosphere. Solid DAC systems use absorbent filters that chemically bind to the CO2. Once heated, they release concentrated CO2, which can be captured and then stored or re-used.
transportING CO2
The CO2 must then be transported to a storage facility, sometimes hundreds of kilometers away. CO2 transport is not particularly difficult and is already widely practiced on an industrial scale by both boat and gas pipeline. For the needs of the oil industry, it is transported in gas pipelines in supercritical state (at ambient temperature and at pressures over 73 bars), which requires the appropriate compression and injection facilities. The USA has a network of 4,000 km of such pipelines. The pooling of CO2 transport and collection infrastructures in major industrial zones, particularly ports, is being considered.
CO2 storage
Once captured and transported, the CO2 must be injected and stored underground. Deep saline aquifers have been identified as the only geological structures presenting adequate capacities to store large quantities of CO2.
Geological storage structures
Two types of structure are in operation:
- deep saline aquifers. These non-potable salt water reservoirs, located deep underground, represent the greatest potential when it comes to storage capacity (400 to 10,000 Gt). They are better distributed around the world than oil and gas fields but their structure and their capacity to trap CO2 over long periods are not as well understood. A major research drive is therefore necessary to assess their geological storage potential and their capacity to confine CO2 over the long term.
- depleted oil and gas fields. This option is interesting since the structures have acted as sealed oil and gas traps for millions of years and the geological environment is relatively well understood. However, their capacities are limited, and often located a long way from industrial facilities. The CO2 will thus have to be transported over long distances. This solution will doubtless be the first to be implemented but it will not be sufficient.
Storage operations in oil fields are already under way within the context of full-scale trials.
Storage capacities
According to the special report on CO2 capture, use and storage published by the IEA in 2020, global CO2 storage capacity is thought to be between 8,000 and 55,000 gigatons. Hence even the lowest figure (8,000 Gt) far exceeds the 100 Gt of CO2 that would have to be stored by 2055 in the “sustainable development” scenario.
The IEA report also says that the land potential is greater than the offshore potential. Land-based storage capacity is estimated to be between 6,000 Gt and 42,000 Gt while offshore capacity is estimated to be between 2,000 Gt and 13,000 Gt, only taking into account sites located less than 300 kilometers from the coast, at depths of less than 300 meters and outside the Arctic and Antarctic zones.
Storage duration and reliability
CO2 storage needs to cover not only the length of time fossil fuels will remain available (1 to 2 centuries) but also the oceanic cycle (around half a millennium). It is vital to take into account the carbon cycle, which is governed by two exchanges: the exchange between the atmosphere and the ocean and the exchange between the biosphere and the atmosphere. While exchanges with the biosphere take place over periods of time measured in decades, the ocean cycle extends over several centuries. In order to stabilize CO2 concentrations in the atmosphere, it is therefore necessary to store CO2 in underground facilities for periods compatible with the oceanic cycle. As a precautionary measure, solutions are being considered that make storage possible over periods of up to thousands of years.
Storage reliability over a long period represents a major challenge. This solution must demonstrate that it is an effective way of tackling climate change (adequate CO2 retention time) and that it does not cause any local environmental damage. Only those sites that present all the safety guarantees will be selected. To do so requires reliable tools to model the future of the CO2 stored, as well as powerful management and surveillance tools that will detect any CO2 that might be leaking so that corrective measures can be put in place.
CO2 conversion: A BETTER SOLUTION THAN STORAGE?
CO2 can be converted for use as a raw material in different industries (chemicals, agrifoods, etc.) or for enhanced oil and gas recovery. It can be converted using chemical and biological processes but the majority of processes under consideration remain at the laboratory or pilot stage. Their profitability and environmental footprint still have to be validated, taking into account a number of criteria: the value of the CO2 market, the volume of CO2 that can be treated, the concentration and purity of CO2, the possibility of using non-greenhouse gas-emitting and low-cost energy to transform CO2, the proximity of CO2 emitting sites and potential conversion sites, life cycle analyses of the converted products, etc.
Direct CO2 conversion
CO2 is currently used for enhanced oil recovery (EOR), which represents less than 50 million tons of CO2 per year, as well as in a variety of industries for applications generally requiring a basically pure gas. This industrial use requires limited quantities of CO2, i.e., no more than 20 million tons annually. Applications include water treatment and the production of fizzy drinks, drugs, refrigerants, and dry ice for extinguishers. Supercritical CO2, an intermediate state between solid and liquid, is used in solvent manufacture.
The chemical conversion of CO2
CO2 is used to produce urea, a nitrogen fertilizer, which represents a consumption of 100 million tons per year, as well as salicylic acid, from which aspirin is derived. CO2 can also be used in the manufacture of some plastic materials such as polycarbonates (lenses for glasses, contact lenses, etc.) and polymethanes (rubbers, foams, etc.). CO2 is also used to harden concrete, via mineralization and carbonation processes.
Another emerging use is the manufacture of products with an energy value and particularly synthetic fuels (e-fuels), obtained by combining CO2 with hydrogen produced by the electrolysis of water using renewable electricity, or more generally decarbonized. Power to Fuel, Power to Gas and Power to Liquid are terms used to refer to processes implemented to convert surplus electricity generated from intermittent renewable energies (wind and solar) into synthetic gas and liquid fuels. The list is long and includes numerous intermediates, from green and renewable hydrogen and synthetic methane, to synthetic ammonia, e-methanol, e-kerosene and e-diesel, etc. If the CO2 used is produced from biomass, the result is an e-biofuel, an advanced biofuel.
Synthetic methane (obtained via the methanation of CO2 or the Sabatier reaction or the hydrogenation of CO2 to methane) could then be injected into existing natural gas networks. Unfortunately the technology is not yet economically profitable.
Biological CO2 conversion
CO2 can be biologically converted by photosynthesis via the production of micro-algae that can grow and consume large quantities of CO2. Currently, these micro-algae profitably produce pigments and omega 3 and could one day produce high added-value molecules for the specialty chemicals sector, the cosmetics and pharmaceutical industries and the animal feed sector. The production of biofuels using this micro-algae-based biological process is even being considered as a potential option in the more distant future.
Chemical and biological conversion processes are currently still at the laboratory or pilot stage.
Numerous industrial players are interested in CO2 conversion and are examining different options: mineralization processes (Skyonic, Calera, etc.), polycarbonate production (Bayer, Novomer, etc.), methanol via direct hydrogenation (Carbon Recycling International, Mitsui Chemicals Inc., etc.).
While the use of CO2 may be of economic interest in the future, questions still need to be asked concerning the potential benefits from a climate point of view. The fact is that, with the exception of CO2 mineralization, products resulting from CO2 conversion only store it temporarily before releasing it back into the atmosphere. However, some of these products have a beneficial effect - albeit to a limited extent -, related to the substitution of a product using fossil carbon. The CO2 used still needs to be biological, and thus already neutral from a climate point of view.
According to IEA estimations, CO2 conversion only represents 8% of the reduction potential attributed to CCUS for the period 2020-2070.