Fuels
Our solutions
Summary:
- Gasoline production and purification
- Distillate production and purification
- Heavy feed conversion processes
- Fuel formulation
Gasoline production and purification
IFPEN develops eco-efficient technological solutions to:
• purify gasoline cuts and adapt them to regional challenges
• foster the coupling of refining with petrochemicals, using oil feed conversion flows to improve the competitiveness of refining sites and accompany their adaptation to an evolving market.
Gasoline hydrodesulfurization processes and catalysts
IFPEN's R&I teams are developing new products and optimizing existing technological solutions to accompany the roll-out of increasingly stringent specifications in terms of air quality.
“A new Prime-G+ gasoline hydrodesulfurization process has been developed to adapt it to the expectations of the two principal markets:
- the USA, where the tightening-up of specifications for sulfur (US Tier 3 standard in 2020) means refining facilities need to be remodeled. Our process design makes it possible to limit the investments required to adapt existing units,
- Asia, and particularly China, where compliance with new standards goes hand in hand with a major constraint with respect to fuel octane levels. Here too, our process addresses this specific need, since it offers maximum octane retention while eliminating sulfur impurities."
Antoine Fécant, chef de projet, IFPEN
In 2021, 300 Prime-G+® units are being operated around the world, producing ultra-low sulfur gasoline meeting the strictest environmental regulations.
Innovative catalytic reforming catalysts and processes
The technologies developed are aimed at improving the quality of fuels to make their use more efficient. Catalytic reforming is an essential step to convert light cuts from crude oil into fuel formulations. The high-performance catalysts in Axens’ Symphony® range, developed as a result of IFPEN’s research activities, are used to produce high-octane gasoline. Their superior performance leads to enhanced process efficiency and hydrothermal stability, extending their lifespan.
Symphony®: 4 types of catalysts and more than 170 references A success that is based on the implementation of new concepts in the formulation of the catalyst supports and active phases.
Distillate production and purification
IFPEN develops processes and catalysts to produce more environmentally-friendly fuels for the road transport and aviation sectors in order to improve air quality and proposes concrete solutions in the fields of:
• diesel hydrodesulfurization
• the hydrocracking of heavy cuts
Hydrotreating catalysts and processe
In order to produce cleaner fuels while reducing the environmental impact of processes, the refining industry needs access to ever more efficient catalysts. This constant optimization is made possible through innovation in terms of materials and the active phases of heterogeneous catalysts, areas that have been at the heart of progress made over the last 20 years or so.
This innovation is hinged around:
- theoretical research, aimed at gaining a better understanding of and rationalizing the fundamental concepts governing catalyst reactivity,
- as well as experimental approaches at the cutting-edge of analysis, catalysis and process experimentation technologies.
This is the type of approach that enabled IFPEN to develop the process for the production of hydroprocessing catalysts containing additives, Impulse® catalysts (hydrotreatment of diesel, hydrocracking of vacuum distillates), in partnership with TotalEnergies and Axens.
The major steps in the design of a new catalyst:
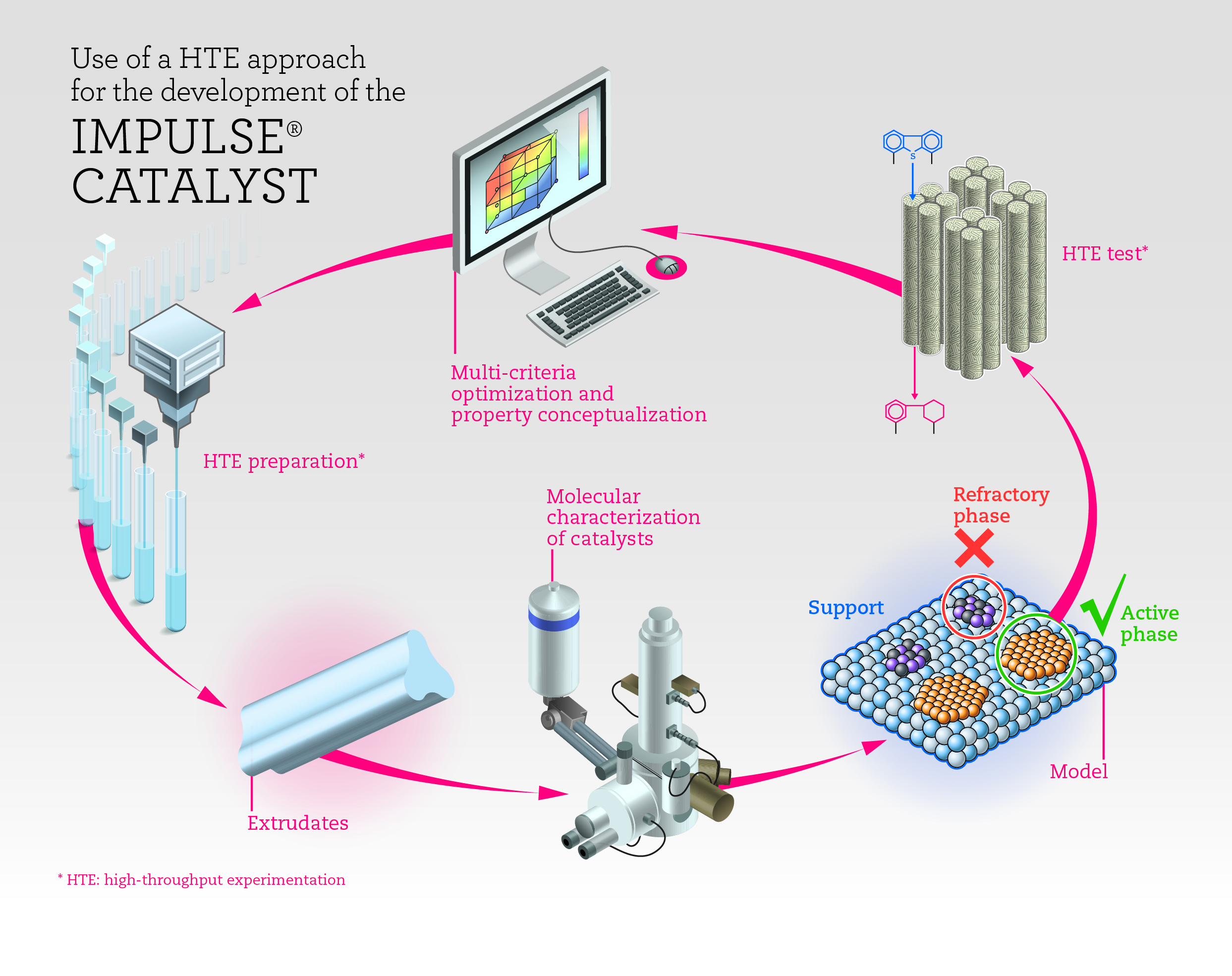
Several other hydrotreatment technologies have also been developed (Prime-D™, HyC-10™, Craken™, HYK™)
Hydrocracking process simulator
In order to operate processes with the best compromise between performance, production costs and environmental impact, it is vital to have access to simulators making it possible to describe and predict industrial behaviors.
“The new So’Crack simulator makes it possible to predict the performance of a hydrocracking process with a view to proposing the best possible catalyst chain. We can now count on a marked improvement in performance predictions, making it possible to ramp up the implementation of the process and propose innovative catalyst chains that fully exploit the synergies of the different catalytic functions. This result was made possible thanks to the efforts of our researchers in the fields of advanced analysis, process modeling and applied mathematics.”
Emmanuelle Guillon, project manager, IFPEN
Technological equipment: distributor platforms
Reactor technologies are essential for maximizing the catalytic efficiency of refining processes. The creation of new designs, such as that of the Hyquench distribution platform, Equiflow™, draws on a combination of process engineering and fluid mechanics expertise.
Learn about the operation of distributor platforms:
Heavy feed conversion processes
IFPEN develops technologies aimed at facilitating the final conversion of the heaviest residues while reducing the environmental impact of processes, and ensuring compliance with environmental standards and constraints, particularly the tightening up of specifications governing bunker fuels since 2020 (IMO).
Combining refining and petrochemicals
The FCC (Fluid Catalytic Cracking) cluster consists of the pretreatment of the FCC feeds and the FCC process itself (R2R™), which treats an average of 25% of a refinery's flow. It is being developed as part of the FCC Alliance, established 35 years ago by IFPEN, Axens, TotalEnergies and Technip Energies (formerly Technip FMC). Research conducted in recent years has made it possible to increase the flexibility of the new fluidized bed catalytic cracking process in terms of feeds and target products with a view to meeting the combined needs of the refining and petrochemicals sectors, while reducing their environmental impact. The research conducted will make it possible to steer cracking towards petrochemicals on a larger scale in order to maximize light olefin production.
"The market success enjoyed by the Alliance, the global leader in the field, is hinged around our experimental strengths built on pilot tests, technological developments (hydrodynamic study models) and advanced analytical tools, a pool of resources not found anywhere else in the world. The FCC Alliance’s framework contract was renewed at the beginning of 2019 for a period of 5 years."
Anne-Claire Pierron, FCC project, IFPEN
IMO specifications for marine fuels
International Maritime Organization (IMO) governing marine fuels since 2020 represents a major change in the refining sector. These regulations are set to have a substantial impact on the way unrefined residues are managed, reinforcing the needs for deep conversion in order to eliminate the production of these sulfur-laden products.
“New IMO regulations impose more restrictive specifications for marine fuels since 2020: their sulfur content is now below 0.5% in order to limit sulfur oxide (SOx) emissions, which are harmful to health. This should lead to a considerable improvement in air quality. These standards reinforce the need for residue conversion and hydrodesulfurization processes. To address this, we are working to improve the H-Oil™ process, which already offers conversion rates in excess of 98%, in order to optimize its economic and environmental performance. We have also developed an innovative process enabling the simultaneous production of an ultra-low sulfur marine fuel and high-value distillates: thanks to the integration of desulfurization and conversion operations, its energy and economic efficiency have been optimized.”
Wilfried Weiss, project manager, IFPEN
Fuel formulation
Find here the solutions offered by IFPEN to optimize fuel use.