CO2 capture, utilization and storage
Our solutions
IFPEN develops innovations across the CCUS value chain:
CO2 CAPTURE
In post-combustion : DMX™ process with demixing solvent
The DMX™ process is dedicated to capturing the CO2 in the emissions of industrial facilities: coal-fired power plants, cement plants, steel works, etc. The idea is to improve the performance of traditional amine-based processes, which consume a significant amount of energy for solvent regeneration. Energy savings of between 30 and 40% are expected. Our solution is based on a high cyclic capacity solvent that decants in two phases, with only the CO2 rich phase sent to regeneration. The chemical stability of this last phase also makes it possible to operate this regeneration at a modified temperature and thus produce CO2 at a pressure (up to 6 eff.bar.). Consequently, it is possible to save two compression stages compared to traditional processes. The tests conducted on a mini-pilot facility at our Solaize site demonstrated the efficiency of the DMX™ process on a small scale and on synthetic gas. We have now launched an industrial-scale demonstration on steel industry exhaust gas, in partnership with ArcelorMittal, TotalEnergies and Axens.
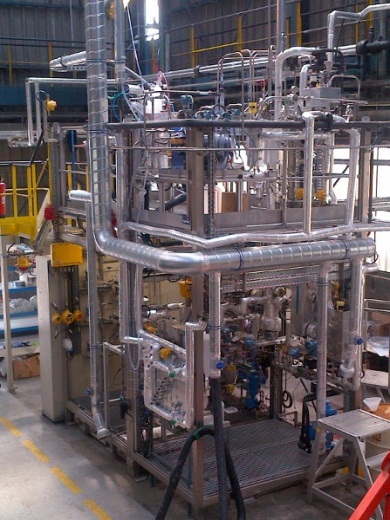
In oxycombustion : chemical loop combustion
IFPEN is developing an innovative CO2 capture process using Chemical Looping Combustion, or CLC. The research has been conducted in partnership with Total (becomed TotalEnergies) since 2008. Large-scale performance is the subject of the Chinese-European H2020 CHEERS project.
Chemical looping combustion consists in concentrating the CO2 directly in combustion flue gases (concentration above 90%) to make it easier to separate from other components. To do this, a metal oxide is used that, on contact with the feed (natural gas, coal, petcoke, biomass, etc.), releases the oxygen required for combustion, producing effluents made up of steam and CO2 alone: it is then easy to isolate the CO2 simply by condensing the steam. The great advantage of the process is being able to achieve this separation without the need for an additional step. As such, its energy footprint is superior to that of its competitors. This research has been the subject of numerous patents and] has been validated using several cold models and on a 10kW pilot unit. It benefits from the expertise of IFPEN's teams in fluidized beds and materials.
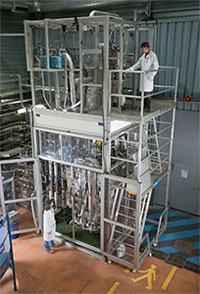
CO2 STORAGE
Securing CO2 storage: CooresFlow simulation software
The CooresFlow research software is an integrated multi-physics, multi-scale simulation solution covering all the stages in the lifecycle of a storage facility. It has been developed in partnership with an oil company and a gas storage company.
CooresFlow is used to simulate fluid flows, transport of chemical species via these fluids and also the interactions between the rock and fluids. This makes it possible to predict:
- the evolution of fluid composition and the porous medium,
- its impact on flows.
This software stands out on the market on several fronts:
- its integrated interface, making it possible to create a model, launch a simulation and visualize the results,
- its flexibility,
- and its calculation performance: it supports complex meshing with potential refinement over time.
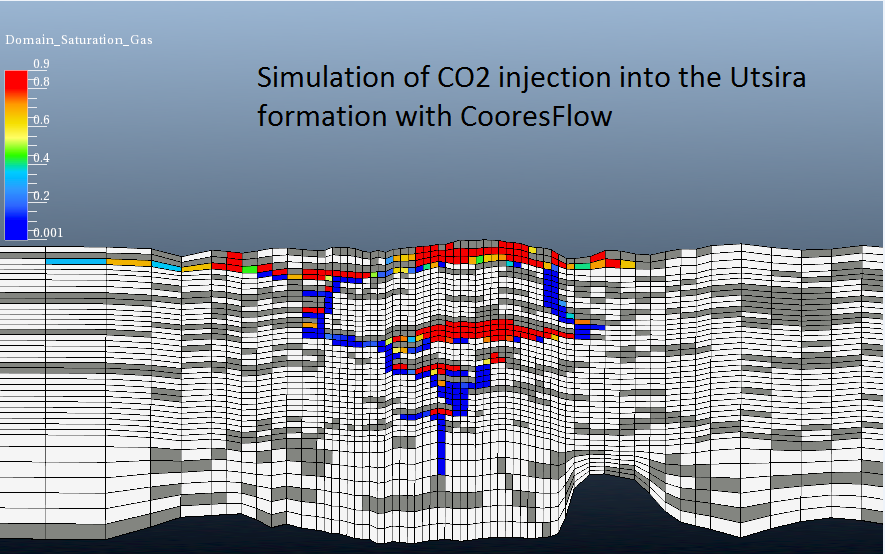
Its broad scope of application makes it suitable for use in the laboratory and out in the field; from well scale, through to site or even basin scale.
CooresFlow can be useful:
• in the storage site selection and design phases, in order to limit risks,
• in the surveillance phase during and after the injection phase, to help position the monitoring tools, adapt the frequency of measurements or simulate the future of the CO2 stored by updating the reactive transport model from these measurements.
CO2 storage monitoring
IFPEN is developing technologies for monitoring CO2 storage sites in the framework of various French and European research projects.
-
Deep leak detection: downhole sampler and analysis booth
The tools developed by IFPEN and its industrial partner SEMM Logging allow to calculate the geochemical composition of a fluid at different locations in aquifers or reservoirs, without needing to take a large number of samples.
The calculation takes place in three stages:• Taking a sample of fluid at a given depth with a downhole sampler, operating at depths ranging from 200 meters to up to 3,500 meters in a well,
• The transfer of the fluid into the T555 transfer cell for the analysis of the gas composition by a micro-chromatograph directly on site:
• Data analysis and interpretation carried out using a thermodynamic model developed from the IFPEN thermodynamic database, which makes it possible to anticipate the composition analyzed under other conditions of temperature and pressure of the reservoir.
-
Shallow leak detection: multi-gas monitoring station
To address the specific challenges of shallow aquifers, potable and potentially potable groundwater and the soil (UZ or Unsaturated Zone), a fixed multi-gas monitoring station has been developed. It is intended to monitor the emission rates of CO2 and other gases on the ground. Its function is twofold:
• to measure the baseline of a site before the start of any industrial or agricultural activities,
• and to monitor the evolution of CO2 emissions.
This continuous monitoring equipment offers a multi-parameter, multi-tracer approach. The station was tested and validated in one of the gallery cavities of the Saint-Émilion natural site as part of the ADEME Demo-CO2 project, in partnership with Bordeaux INP. This equipment is also used to monitor an unclassified aquifer in the context of the Aquifer-CO2Leak project.
CO2 CONVERSION
CO2 can be considered as raw material to produce other molecules. IFPEN, through the Sun2Chem project, is participating with its partners in the development of a process to obtain ethylene from CO2, using solar energy.